I have experience in accident investigations, root cause analysis, confined space entries, OSHA standards, recordkeeping, powered industrial truck operations, and warehouse logistics. I have also testified in both plaintiff and defense litigation matters.
OSHA Authorized General Industry Trainer for ten and 30-hour courses. Conducts safety audits and assists clients in developing and implementing their safety programs. Contact Construction Safety Expert now!
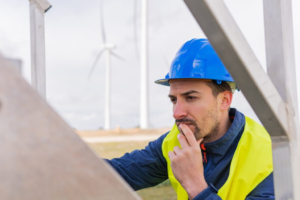
OSHA develops, trains, and enforces safety standards. It also investigates probable causes of work-related sickness, injuries, and death. Failure to comply with the agency’s standards can result in fines and legal repercussions. In addition to making sure workers are fully trained, the agency provides compliance assistance tools and training to help employers meet the standards.
Under the Occupational Safety and Health Act (OSH Act), Congress gave OSHA broad authority to set workplace health and safety regulations called standards. To create a standard, the agency must first consult with representatives of industry and labor, as well as gather whatever scientific, medical or technical data is necessary to ensure that the new rule accurately reflects workplace realities. Then, the proposal must go through a lengthy comment period before it is finally approved as a legally binding standard.
Once a standard is in place, OSHA enforces the rule by conducting inspections and investigating complaints from workers and others. Each inspection is conducted by a trained compliance safety and health officer who checks whether an establishment complies with the OSHA standards. The agency inspects all workplaces that are covered by the OSH Act. For states that operate their own OSHA-approved job safety and health programs, federal OSHA oversees the state programs to make sure that they are at least as effective as the federal program.
OSHA staff also works with organizations and businesses, such as trade and professional groups, unions, employers associations, educational institutions, community and faith-based organizations and governmental agencies, through its Alliance Program. The goal is to improve workplace safety and health by providing assistance in meeting the OSHA requirements, including developing and delivering training, providing guidance on compliance issues, sharing best practices and supporting innovation in safety and health management.
OSHA offers special flexibility for small firms that may have limited resources to meet some of the stricter standard requirements, such as emergency evacuation procedures and process safety management. The agency allows these firms to receive penalty reductions of 60 percent if they prove that they have established and implemented effective safety programs for their employees.
OSHA Training
The Occupational Safety and Health Act (OSH) charges OSHA with assuring that workers have safe and healthful conditions in their workplace. The agency is small and cannot physically visit all workplaces, so it tries to reach workers by providing training to help them understand their rights and responsibilities under the OSH Act. The agency also tries to make the law easier to understand and enforce by providing information in a language and vocabulary that workers can understand.
In addition to its website, OSHA provides training for workers and employers through regional offices and the OSHA Training Institute Education Centers. These centers offer courses in workplace safety, safety and health topics for employees at all levels of the workforce. Courses cover topics such as recognizing hazards, using the equipment properly and safely, managing hazardous chemicals, preventing fires and other safety-related concerns.
For example, one of the most popular OTI courses is the 10-Hour Construction course, which helps workers to recognize common construction hazards and learn how to avoid them. OSHA researchers have identified four construction hazards that cause a significant number of fatal injuries: falls, caught-in or between hazards, struck-by hazards and electrocution. Those who take the course receive a certificate of completion right away and an OSHA card that they can use to seek or maintain employment in the industry.
Another type of OTI training is the 5-Hour Fall Hazard Recognition course, which teaches workers how to identify and assess fall hazards on a jobsite. It covers issues such as scaffolding, identifying unsafe work positions and determining proper egress from a working surface. The course also discusses how to properly assemble, disassemble and use scaffolding and identifies types of scaffolding and their capacities.
Other OTI courses include the Basics of Construction Safety, which is designed for those new to construction. It provides an overview of OSHA’s construction standards and explains the roles and responsibilities of the employer, worker and supervisor in compliance with these standards. The Basics of Construction Safety also focuses on the construction industry’s most common violations of safety and health regulations.
OSHA Inspections
OSHA inspectors often make unannounced visits to a construction site. They usually spend about three to four hours at a facility. During the inspection, the compliance officer will conduct an opening conference, a walk-through of the facility and a closing conference.
During the opening conference, the inspector will explain why they are there and what their scope of authority is. They should also state whether they are responding to a complaint or conducting a programmed inspection. If they are responding to a complaint, the company coordinator should request a copy of the complaint. If they are conducting a programmed inspection, the company coordinator should ask for a schedule or program that specifies when their facility will be inspected.
The company coordinator should then designate someone who will greet the inspector and present their credentials. The inspector should be asked to validate their credentials, which will contain a photograph and serial number. The coordinator should also verify that the compliance officer is properly licensed and trained.
While the facility is being inspected, the employer should ensure that employees are not being disturbed or interrupted. The inspector will walk through the facility, taking notes and photographs. The inspector will interview employees and may suggest changes to safety protocols or equipment. The inspector will also take samples of air, water and surface materials for testing.
During the closing conference, the inspector will summarize their findings and address any questions or concerns that have arisen during the inspection. They will also discuss any citations that might be issued. The inspector will describe the nature of each violation and recommend a timeline for correction. If the citations are not corrected by the specified date, OSHA will issue a penalty amount.
After the closing conference, the company should show records of their efforts to correct any violations identified during the inspection. They should also indicate how long they expect it will take them to correct the remaining violations. They should be prepared to negotiate a penalty amount with the inspector if necessary. If they are unable to reach a reasonable agreement, they should seek legal counsel for assistance with contesting the penalties.
OSHA Citations
A single violation of Occupational Safety and Health Administration regulations can cost your company thousands of dollars. Even more important, it could damage your reputation and hurt employee morale. To ensure that your workplace complies with federal standards, you need a team of Construction Safety Experts to develop and implement a comprehensive program. The goal should be to identify hazards and take steps to prevent them from occurring, which will help you avoid costly citations and penalties.
The most common OSHA violations are failure to post a warning sign or use the proper PPE (personal protective equipment). Other common citations include failing to provide adequate lighting, electrical outlets and locks on toolboxes, improper use of ladders, scaffolding or shoring, exposure to airborne contaminants above the permissible exposure limit, inadequate recordkeeping, improper training for crane operators, and lack of worker access to fire extinguishers.
If the alleged violation is deemed serious, it can result in a monetary penalty of up to $161,323 per instance. This is the highest fine for any type of violation, and it’s one of the main reasons that it’s important to have a team of Construction Safety Experts on your side.
An employer can mount an affirmative defense against any citation issued by a CSHO. Affirmative defenses must be proved at the time of the hearing, but CSHOs should preliminarily gather evidence that would support any such defenses.
On multiemployer worksites, CSHOs will typically conduct separate inspections at each establishment. If instances of the same serious hazard are discovered at different establishments, however, they may not be grouped.
A hazard is considered recognized if the employer has actual knowledge of it. This can be established by a variety of evidence, including written or oral statements by management and/or supervisory personnel, company memorandums, work rules that specifically identify a hazard, operations manuals, safety records, workers’ compensation data, or past accidents/incidents.
OSHA focuses its efforts on those worksites that most need help to improve the safety and health of their employees. As part of its reinvention, the agency has reorganized its area offices to respond more quickly to worker complaints and to focus on long-term strategies to reduce job-related deaths and injuries. The agency has also instituted a phone-fax complaint-handling policy to speed up resolution of complaints and to help focus resources on the most serious violations.